In the world of manufacturing and packaging, the efficiency and safety of products heavily rely on the quality of seals. Poor seal quality can lead to product contamination, spoilage, and customer dissatisfaction. This article delves into the various aspects of seal inspection, a crucial process that ensures the integrity and safety of products. Discover the techniques, benefits, and challenges associated with seal inspection in manufacturing.
To gain an in-depth understanding of the cutting-edge technology used in seal inspection, click on this seal inspection link.
What is Seal Inspection?
Seal inspection is a quality control process used in manufacturing to evaluate the integrity of seals on packaging materials. This process is vital for ensuring that products remain safe, fresh, and free from contaminants. Seal inspection typically involves the use of advanced technologies such as vision systems, sensors, and automated equipment to detect any defects or irregularities in seals.
Key Techniques in Seal Inspection
The techniques used in seal inspection can vary depending on the type of product and packaging material. Some of the most common methods include:
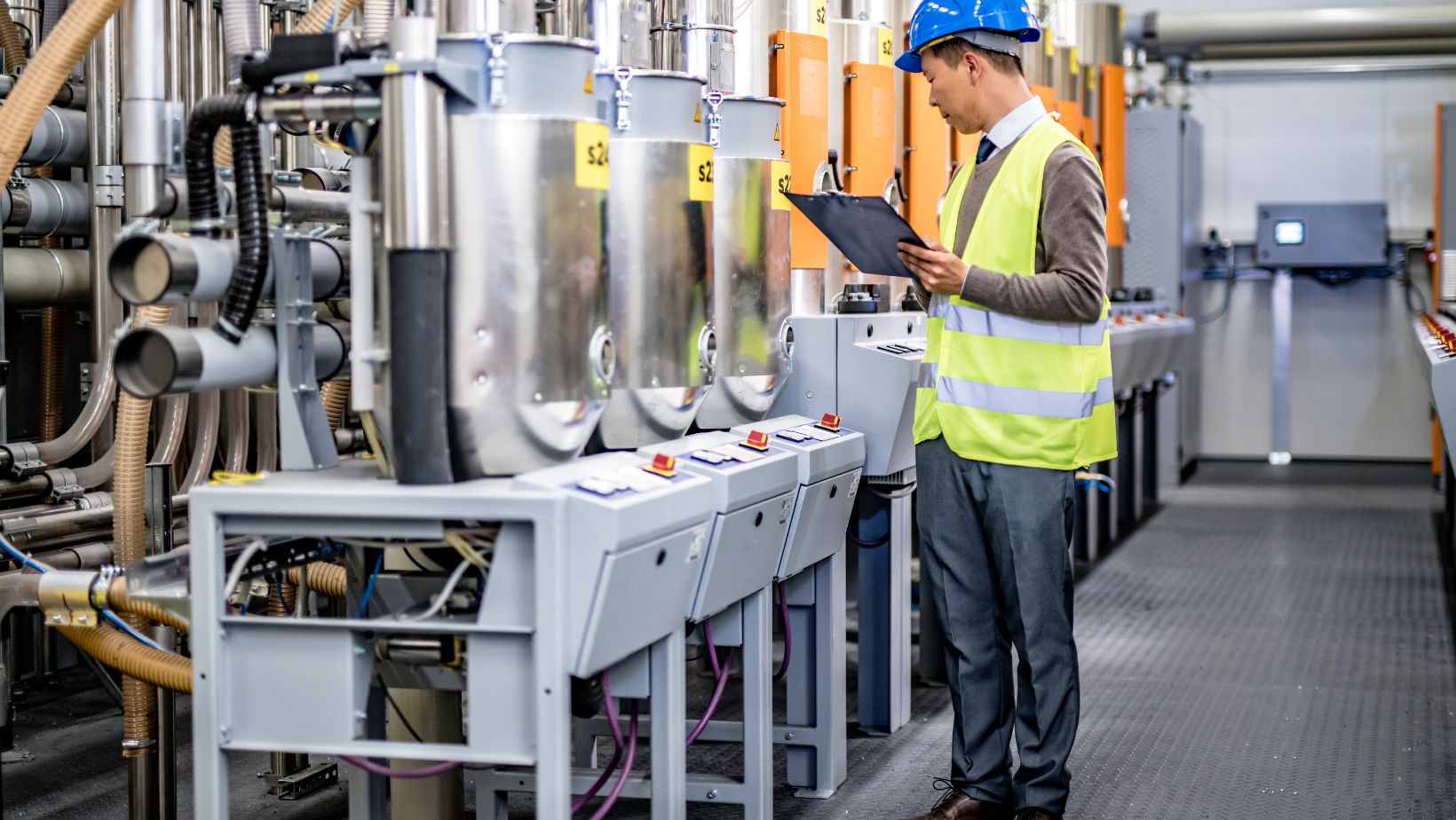
- Visual inspection: This involves the manual or automated visual assessment of seals to identify visible defects such as gaps, tears, or misalignments.
- Pressure decay testing: This method checks for leaks by measuring the pressure drop in a sealed package over time.
- Vacuum testing: A vacuum chamber is used to detect leaks by observing changes in pressure when a vacuum is applied.
- Infrared and ultrasonic testing: These non-destructive testing methods use infrared and ultrasonic waves to detect inconsistencies in seal quality.
Benefits of Effective Seal Inspection
Implementing a robust seal inspection process offers numerous advantages, including:
- Ensuring product integrity: Accurate seal inspection helps maintain product quality by preventing contamination and prolonging shelf life.
- Reducing waste: By identifying defective seals early in the production process, manufacturers can reduce waste and improve efficiency.
- Enhancing consumer trust: Consistently providing products with intact seals builds consumer trust in the brand and its quality control processes.
- Compliance with regulations: Adhering to seal quality standards ensures compliance with safety and quality regulations in various industries.
Challenges in Seal Inspection
Despite its importance, seal inspection poses several challenges, such as:
- Variety of packaging materials: Different materials require different inspection methods, complicating the inspection process.
- Complex seal designs: Intricate seal patterns can be difficult to inspect thoroughly, increasing the risk of overlooking defects.
- Environmental factors: Temperature and humidity variations can affect seal integrity, necessitating continuous monitoring.
- Balancing cost and accuracy: Investing in advanced inspection technologies can be costly, making it challenging to balance cost with inspection accuracy.
Future Trends in Seal Inspection
As technology continues to evolve, seal inspection methods are expected to become more advanced and efficient. Future trends in seal inspection include:
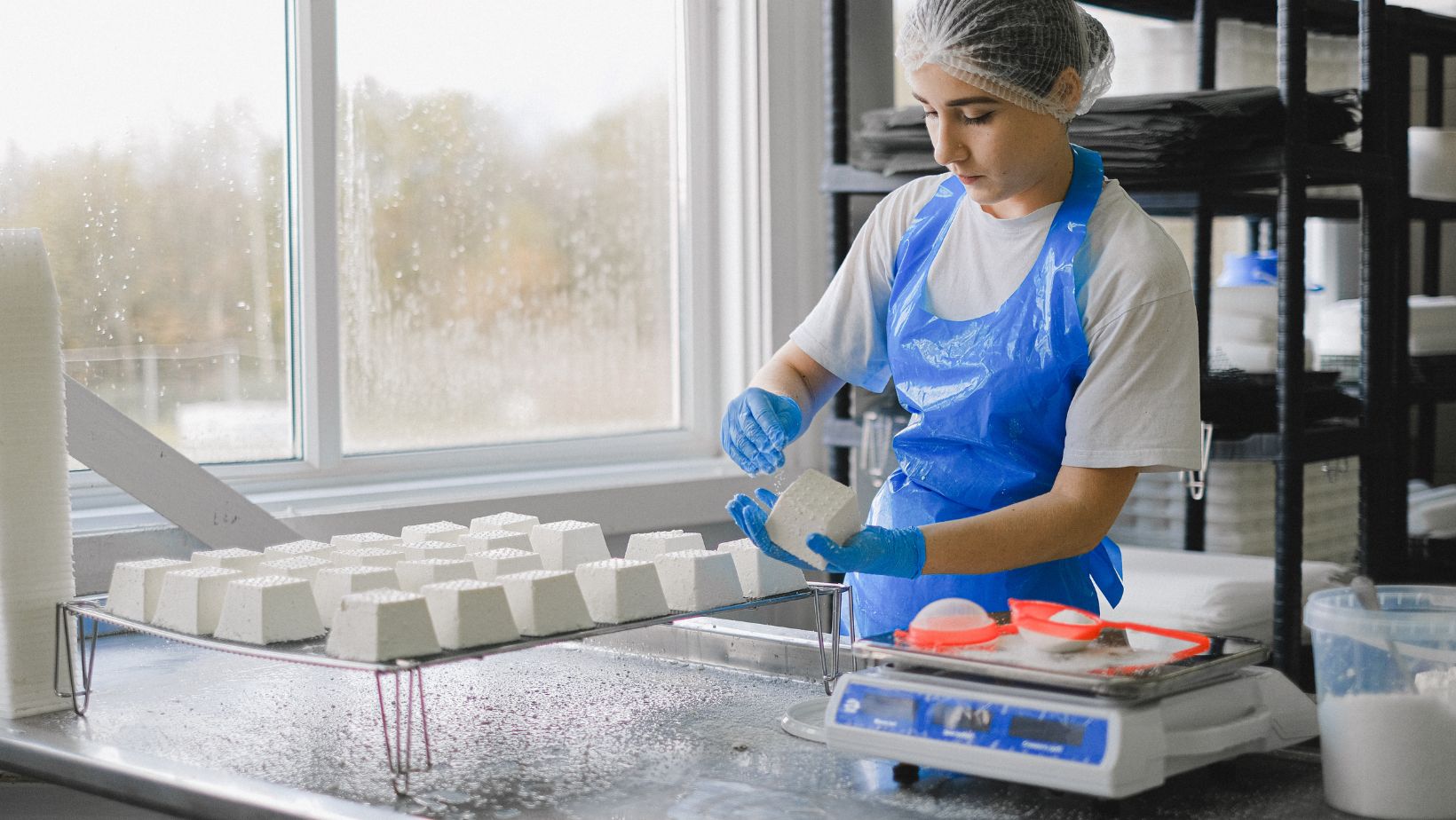
- Integration of artificial intelligence: AI-powered systems can enhance inspection accuracy by learning from data and improving defect detection capabilities.
- Increased automation: Fully automated inspection systems will streamline the manufacturing process, reducing the need for manual intervention.
- Real-time monitoring: Advanced sensors and IoT devices will enable real-time inspection data, allowing for immediate corrective actions.
Conclusion
Seal inspection is an indispensable aspect of manufacturing that ensures product safety, quality, and consumer satisfaction. By understanding the techniques, benefits, and challenges associated with seal inspection, manufacturers can enhance their quality control processes and stay competitive in the market. As technology advances, the future of seal inspection promises more efficient and accurate methods, further solidifying its importance in the industry.